What’s the first thing you consider when you begin to design a bag? For many people, the answer will be the material. Finding the right fabric is essential to a bag’s success, as it will largely contribute to its durability, quality, and appearance. Thorough research is crucial for both designers and manufacturers, as not all fabrics are equal in terms of quality and characteristics. Conducting comprehensive research helps ensure informed decision-making when selecting fabrics for various applications. Nylon, a strong and versatile synthetic material, is a worthy candidate for many bag varieties. Below we’ll explore everything you need to know about nylon and its application in bag manufacturing so you can figure out if it’s the right choice for your needs.
What Is Nylon?
Nylon, a synthetic polymer, finds widespread use in various industries, including fashion and bag manufacturing. Regarded as one of the most revolutionary textiles ever invented, it has made significant contributions to the field. Developed in the 1930s, nylon was the first synthetic fabric to reach commercial success. It quickly became a popular alternative to silk, as its smooth, lustrous texture acts as a perfect replica of the fabric.
Nylon fibers are produced through a process called polymerization. In this process, raw materials undergo a chemical reaction to form long chains of polyamide molecules, resulting in the creation of nylon fibers. These chains are highly durable and challenging to break apart. This results in a lightweight, durable, and flexible fabric with excellent strength and elasticity, making it ideal for bag manufacturing.
Advantages Of Using Nylon In Bag Manufacturing
- Durability. Nylon is renowned for its exceptional strength, durability, and elasticity. With proper care, a quality nylon bag can last for years to come. Its robust fibers can withstand significant wear and tear, ensuring that bags made from nylon maintain their shape and integrity. Nylon is highly resistant to abrasion and stretching, and it can hold relatively high amounts of weight without tearing apart. It’s an excellent fabric for bags that will endure heavy use.
- Versatility. Nylon offers tremendous versatility in terms of design possibilities. Nylon can be easily dyed, offering a vast array of vibrant color options. Nylon fabrics can also be treated to mimic the appearance and texture of other materials, granting designers abundant creative opportunities.
- Water Resistance. Nylon exhibits superior water resistance and impermeability, which is why it’s a popular choice for travel and outdoor bags. External liquids that fall onto nylon bags will easily roll off the surface, and the fabric’s inherent moisture-wicking properties allow it to dry quickly and protect any internal contents. Bag manufacturers can further enhance nylon’s water-repellent properties through added external coatings.
- Mildew, Fungi & Insect Resistance. In addition to repelling water, nylon is also resistant to molds, mildew, fungi, and insects. It’s an ideal fabric to withstand humid and/or tropical environments.
- Lightweight. Nylon’s lightweight nature is advantageous for manufacturers and consumers. It produces some of the lightest bags on the market, ensuring comfort. This feature is particularly beneficial for travel bags and backpacks, where weight considerations are important.
- Easy Maintenance. Nylon bags are easy to maintain since dirt does not adhere to their surface. Nylon is easy to machine wash or wipe clean. Nylon’s resistance to wrinkles and creases ensures that bags retain their shape and appearance with minimal care, and its moisture-wicking properties mean that dry times are fast.
Limitations of Using Nylon in Bag Manufacturing
- Heat Sensitivity. Nylon tends to be more heat-sensitive than other synthetic materials. It is important to exercise caution when exposing nylon bags to heat sources as high temperatures can cause the fabric to melt or deform.
- Bleach & Acid Sensitivity. Exposure to bleach should be strictly avoided as it can cause the nylon to melt. Additionally, other acidic chemicals can also lead to the breakdown or damage of nylon fibers.
- Dye Sensitivity. While nylon’s ability to easily pick up colors is a benefit during the production process, it can cause end-user issues. When washing nylon bags, consumers should exercise caution to prevent the transfer of dyes from other items onto them.
- Environmental Impact. Nylon is derived from harmful petrochemicals, which raises concerns about its environmental impact. However, sustainable alternatives such as ECONYL® have been developed in recent years.
Nylon Production & Manufacturing Considerations
Nylon bag manufacturers should invest in specialized cutting tools, such as sharp blades or rotary cutters, to create precise and clean cuts. Sewing machines equipped with features suitable for nylon, such as Teflon-coated or roller presser feet, help reduce friction against the fabric and provide smooth stitching. To ensure secure seams and prevent damage during production, it is advisable to use nylon-specific needles and thread when working with nylon materials.
Nylon Sustainability & Environmental Impact
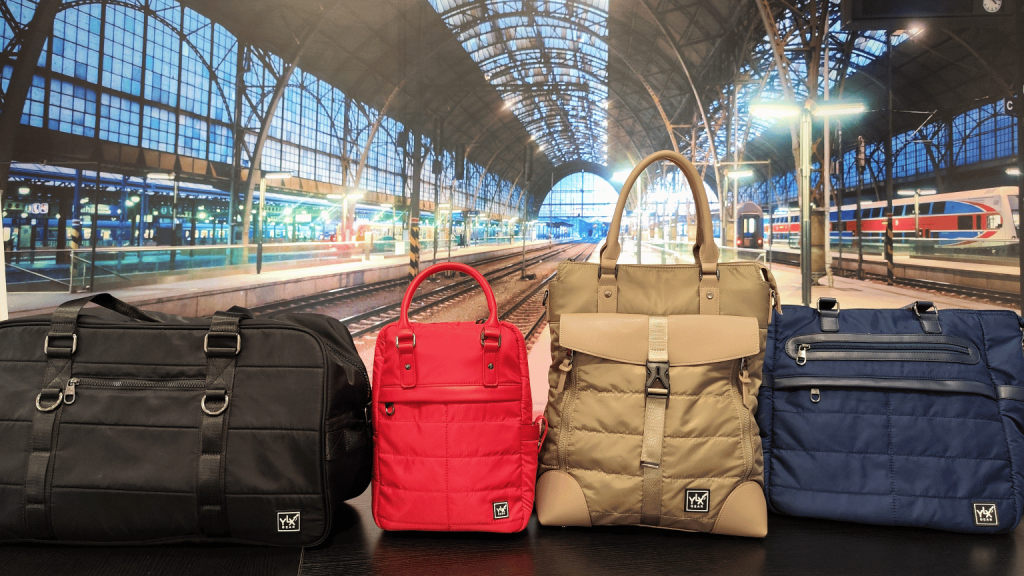
Nylon typically does not have a clean slate when it comes to its environmental impact. Conventional nylon is derived from non-renewable petrochemicals. The extraction and processing of these fossil fuels contribute to greenhouse gas emissions, air pollution, climate change, and environmental degradation.
The production and manufacturing process itself involves energy and water-intensive operations which further release pollutants. The disposal of waste materials generated during production, such as chemical solvents and byproducts, also presents environmental challenges if not properly managed.
Fortunately, the industry has been working to overcome these issues. Recycled nylon, known as ECONYL®, has been a game-changer within the industry. The innovative solution repurposes waste materials such as discarded fishing nets, industrial plastic, and post-consumer products to create a more sustainable alternative to conventional nylon. By recycling and regenerating these materials, the production of recycled nylon reduces the need for virgin materials and diverts waste from landfills and oceans.
The adoption of eco-friendly production practices also helps mitigate nylon’s negative environmental impact. Manufacturers can reduce their carbon footprint by selecting high-quality nylon that will last for years, optimizing energy and water consumption, implementing effective waste management systems, and ensuring responsible chemical usage and disposal to minimize harm to ecosystems.
Conclusion
From a marketing standpoint, brands can also make a difference by promoting conscious consumption and encouraging consumers to carry their bags for as long as possible. Nylon’s durability and longevity make this an easy task. Its inherent strength eliminates the need for frequent replacements, leading to reduced waste from both manufacturers and consumers. With its durable and lightweight nature, nylon is a desirable choice for many bag manufacturers. This versatile fabric can be transformed into almost any design, from trendy shoulder bags to heavy-duty hiking backpacks. Indeed, nylon’s limitations concerning heat sensitivity and environmental impact can be effectively addressed by making thoughtful design choices and embracing sustainable manufacturing practices.