The FLA goes beyond making fair working conditions the standard and not the exception. Written on its website in clear and bold fonts are words such as ”accountability” and ”transparency”. Now entering and celebrating its 25th year, why does the Fair Labor Association stick out? This article will tell you everything you need to know about FLA accreditation and why it’s important.
The bag manufacturing industry has dramatically shifted beyond just the materials used. Now, end-buyers look deeper than just where materials come from. Both designers and manufacturers focus on their products’ entire lifecycle, placing special emphasis on the workforce. Ensuring fair wages and safe working conditions has become a top priority in the industry. This shift towards sustainability and ethical practices highlights these elements’ importance in today’s market. Embracing industry accreditations, like FLA accreditation, is a positive step forward in addressing moral issues.
What Is The FLA?
The Fair Labor Association (FLA) emerged directly from the Apparel Industry Partnership (AIP), initiated by U.S. President Bill Clinton, established in 1996 to address labor rights standards within the apparel industry. The FLA was established in 1999 as a nonprofit by companies, human rights and consumer groups, and university officials. It is dedicated to enhancing workers’ rights in factories both within the U.S. and overseas. Its inception aimed to unify and protect worker rights in the apparel and footwear industries.
FLA: Striving for Fair Labor Practices
The Fair Labor Association (FLA) organizes its board to include representatives from three different categories:
1 Companies
2 Universities
3 NGOs
Each category has equal representation to ensure fair governance and decision-making. This structure highlights the FLA’s multi-stakeholder nature, aiming for collaboration and accountability across different sectors. The association accredits independent monitors and verifies company compliance with its Code of Conduct, which outlines specific worker protection standards. FLA member companies pledge to enforce standards, monitor compliance, and rectify factory non-compliance. Additionally, the FLA provides a platform for public reporting and transparency by publishing the outcomes of factory inspections and monitoring reports.
Purpose and Objectives
The FLA ardently commits to eradicating sweatshop labor and significantly elevating working conditions in global factories. Consequently, through the united efforts of colleges and universities, NGOs, and socially responsible companies, it diligently enforces accountability to the FLA Workplace Code of Conduct among all entities engaged in manufacturing and marketing. Additionally, its goals include boosting transparency, actively encouraging public reporting, and effectively cultivating a culture of compliance and remediation within its member institutions.
Initially, the FLA focused mainly on the apparel and footwear industries. However, its framework for improving workers’ rights is versatile and applies to any goods-producing sector, potentially including electronics, sporting goods, and agricultural products. Any industry aiming to ensure labor rights and ethical manufacturing processes can leverage this certification. The mention of suppliers licensed by U.S.-based colleges and universities to produce mainly sports-related products bearing school logos also hints at the FLA’s engagement beyond traditional apparel, touching upon sectors like collegiate merchandise. Such adaptability underscores the FLA’s versatile approach to improving working conditions and labor rights across various manufacturing landscapes.

Standards and Requirements
The certification process for a bag factory, which primarily aims to ensure compliance with the Fair Labor Association (FLA) standards, involves a series of steps. Initially, this process necessitates the meeting of specific labor rights, working conditions, and corporate responsibility criteria. Following this, the FLA’s code of conduct outlines the key requirements a factory must adhere to in order to obtain certification. These standards are established with the intention to protect workers’ rights and ensure ethical production practices.
- Legal Compliance: Factories must comply with local and national laws, particularly labor, health and safety, and the environment.
- Forced Labor: In order to foster a fair working environment, the factory is compelled to eradicate all manifestations of forced labor. Consequently, workers must be allowed the freedom to select and maintain their employment voluntarily.
- Child Labor: Factories ought to consistently adhere to the minimum age provisions of local laws and thereby avoid employing child labor.
- Harassment or Abuse: Maintaining a workplace that is free from any form of harassment or abuse, including physical, psychological, sexual, or verbal, is imperative.
- Non-discrimination: Employment practices must not discriminate based on race, color, gender, religion, political opinion, nationality, social origin, or any other condition that could give rise to discrimination.
- Health and Safety: Factories must provide a safe and healthy working environment. This includes preventing accidents and injury, ensuring access to clean bathrooms and drinkable water, and offering necessary personal protective equipment.
- Lack of Association and Collective Bargaining: Employers must recognize and respect workers’ rights to form, join, and actively participate in trade unions and collectively bargain.
- Wages and Benefits: Factories must pay wages that meet or exceed the minimum legal or industry standards and provide any legally mandated benefits.
- Hours of Work: Factories must not exceed the maximum hours prescribed by local law, and overtime must be voluntary and compensated at a premium rate.
- Environment: Factories should comply with environmental regulations and take steps to minimize negative environmental impacts.
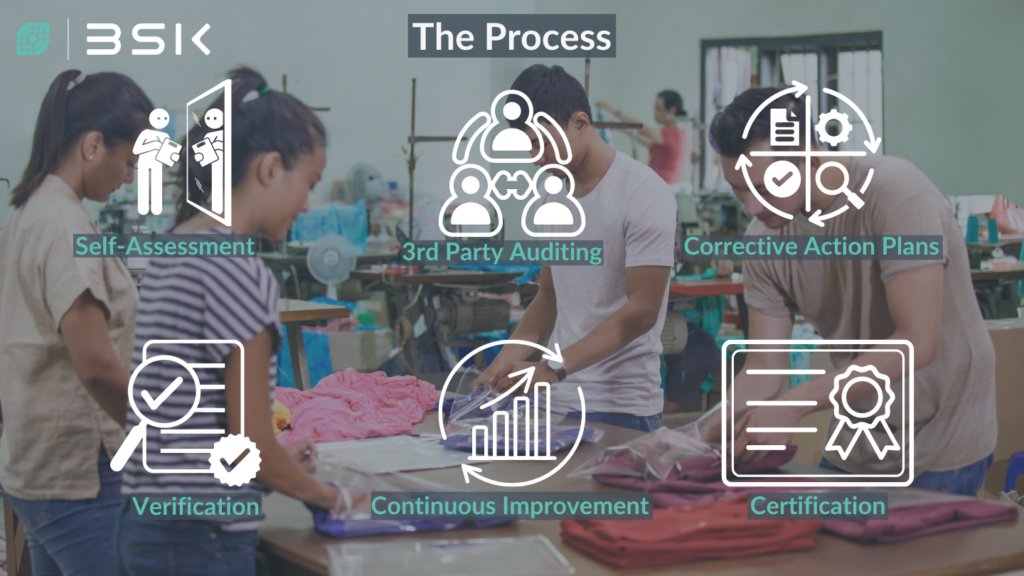
The Process
- Self-Assessment: The initial step involves the factory conducting a self-assessment to understand the gaps between current practices and FLA standards.
- Third-Party Auditing: An FLA-accredited independent monitor conducts unannounced audits to evaluate the factory’s compliance with the FLA code of conduct. This includes interviews with workers and management personnel, as well as document reviews.
- Corrective Action Plans (CAPs): If non-compliance is identified, the factory must create a corrective action plan to resolve the issues found.
- Verification of CAP Implementation: Conduct follow-up audits or checks to ensure the implementation of corrective actions is effective.
- Continuous Improvement: The factory regularly updates and evaluates to maintain compliance and tackle emerging issues.
- Certification: Once the factory has met all FLA standards and implemented the required corrective actions, it receives certification. This certification is subject to review and renewal, contingent on the factory maintaining the FLA standards. The certification process improves factory operations, ensures workers’ rights protection, and enhances reputation with ethically made products.
Benefits and Significance of FLA Accreditation
Achieving accreditation from the Fair Labor Association (FLA) benefits bag factories and the brands they supply. This accreditation elevates their reputation, cultivates customer trust, and opens new market opportunities.
Enhanced Reputation and Brand Value
Recognition of Ethical Practices. FLA accreditation signifies a company’s commitment to high labor standards and ethical practices in its supply chain to stakeholders. This recognition significantly enhances the brand’s overall value and reputation.
Differentiation in the Market. Being affiliated with the FLA distinguishes brands as leaders in social responsibility and ethical manufacturing, setting them apart from competitors.
Increased Customer Trust
Transparency and Accountability: FLA-accredited companies must report publicly on their efforts to improve working conditions. This level of transparency fosters trust and loyalty among consumers who prefer to support brands with ethically produced goods.
Assurance of Product Integrity. FLA accreditation ensures products respect workers’ rights and good labor practices, aligning with socially conscious shoppers’ values.
Market Opportunities and Economic Benefits
Access to New Markets. Initially, adhering to FLA-endorsed labor standards can open market opportunities. Particularly, buyers who demand or prefer compliant suppliers, including universities and corporations, may find this adherence appealing.
Competitive Advantage: FLA accreditation offers strategic advantages in negotiations. Buyers appreciate ethical sourcing and corporate responsibility.
Promoting Sustainability, Responsibility, and Quality Management
Sustainable Business Practices
FLA participation promotes sustainable businesses, reducing labor dispute risks, increasing worker satisfaction, and enhancing productivity.
Improvement in Workplace Conditions.
FLA enhances workplaces and product quality. Additionally, it aims at solving problems which, in turn, benefits workers significantly. Furthermore, this approach fosters a motivated and well-treated workforce.
Leadership in Social Responsibility.
Furthermore, by emphasizing these values, they retain talented individuals committed to upholding ethical standards. By meeting FLA standards, bag factories and their partners underscore their dedication to ethical practices, social responsibility, and effective quality management, which are increasingly important factors in today’s global marketplace.
Industry Relevance of FLA
The Fair Labor Association (FLA) certification holds significant importance within the bag manufacturing industry. Primarily, it reassures consumers and stakeholders about the adherence to ethical labor practices. Moreover, it fosters consumer trust, crucial for brand loyalty. Similarly, FLA certification safeguards brand reputations, a foundational aspect of any company’s success. Additionally, this certification aids companies in meeting regulatory and market expectations, ensuring compliance and competitive edge. Furthermore, practical applications of FLA certification have led to tangible benefits, notably improved worker satisfaction and increased operational efficiency. Consequently, FLA certification is paramount in fostering ethical global commerce within the bag manufacturing sector.
Conclusion
In wrapping up, it’s been an insightful journey diving into the world of certifications for bag factories. The takeaway is loud and clear: there’s immense value in bag manufacturers stepping up to earn these certifications. Not only do they underscore the quality and integrity of their products, but they also shine a spotlight on their commitment to ethical and sustainable business practices. For any bag manufacturer looking to elevate their brand and stand out in a crowded marketplace, pursuing certification is more than just a good business decision—it’s a powerful statement about who they are and what they stand for. So, to all the bag creators, consider this a nudge towards improving and outstanding your business. Let’s put quality, sustainability, and responsibility at the forefront of the fashion industry, one certified bag at a time.